

PET is a hygroscopic material, if the moisture content is too high, will produce at a high temperature hydrolysis process, the PET molecular chains and thermal decomposition of acetaldehyde, reduce physical and mechanical properties, the crystallization rate of speed, when the Preform Injection, will Preform partially crystalline bleaching, affecting the quality of the product. PET is a polymer, the most important feature is its molecular weight, molecular weight is the number of uniform molecular PET molecular chains, the number of molecules of longer chain link, the better the physical properties of PET. PET is a crystalline resin, a specific gravity of about 1.4, a melting point of 245 ℃, the molding temperature between about 290 ~ 315 ℃. Usually used in the manufacture of PET plastic container grain, must pay attention to the following features: (1) molecular weight (2) acetaldehyde content (3) the content of diethylene glycol (4) a carboxyl group (5) the percentage of total polymer ( 6) Melting point (7) a glass transition point (8) the degree of crystallinity. Polyethylene terephthalate (of PET) , having the features: (1) excellent in gas barrier properties (2) pressure resistance, creep resistance (3) Impact resistance (4) transparency, surface gloss (5) itself is odorless and Paul fragrance security (6) on food hygiene, and beautiful, easy molding, has been widely used in food containers.
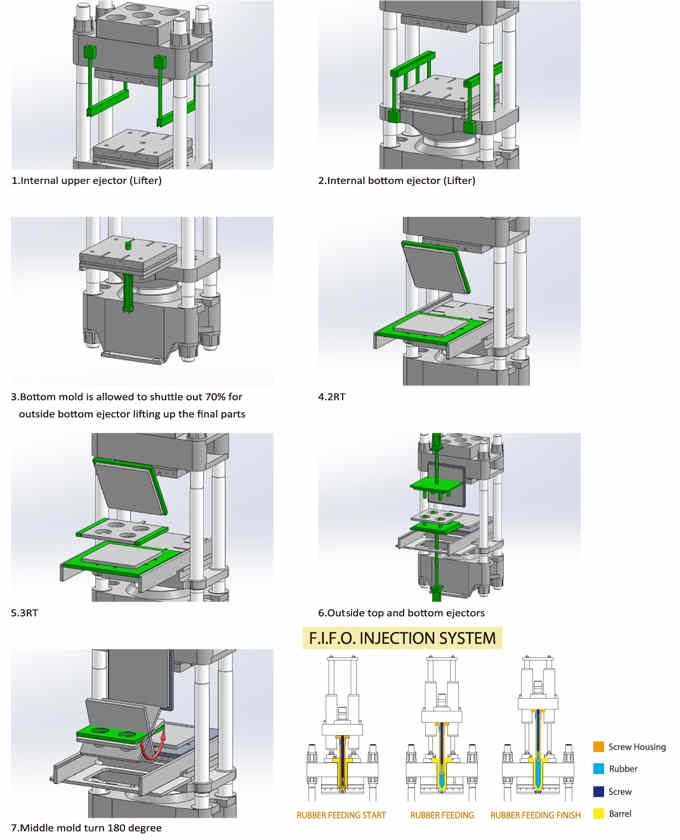
Here are some notes for the PET preform injection molding process, for all my friend, much know-how experience, much near to the perfect production. The final result is that the bad quality &bad production of PET preform in the customer factory, which will waste the money &energy &time of all. And in order to reduce the sell cost, many manufacturers also present the general purpose injection molding machine with C type of screw &big shot weight, while they obviously ignored to bring the important notes to the customer before they make a decision focus on the PET PREFORM PRODUCTION. Var bIsWM = sUserAgent.Many friends would like to adopt the general purpose injection molding machie to produce the PET preform. Var bIsCE = sUserAgent.match(/windows ce/i) = "windows ce" Var bIsAndroid = sUserAgent.match(/android/i) = "android" Var bIsUc = sUserAgent.match(/ucweb/i) = "ucweb" Var bIsMidp = sUserAgent.match(/midp/i) = "midp" Var bIsIphoneOs = sUserAgent.match(/iphone os/i) = "iphone os" Var bIsIpad = sUserAgent.match(/ipad/i) = "ipad" Price is around double for self-locking common preform mold. In this way, it is no doubt that the mould can be used for 2 million shots without any maintenance, meanwhile, the wall thickness difference between is not more than 0.10mm (length<=100mm), weight difference is less than 0.3g turning center processes make sure that every mould parts can match very well to ensure mould concentricity Proper distribution of cooling water system improve productivity effect and molding cycle only takes 15seconds. Mould is produced automatically to save labor force. So some old traditional problems such as left white marks or drawbench on bottom are easily avoided. This kind PET Preforms mold adopts the valve gate(shut-off) design, in which each cavity has its own heating zone and temperature is measured by independent thermo couple. The Third generation is self-locking penumatic preform mold.
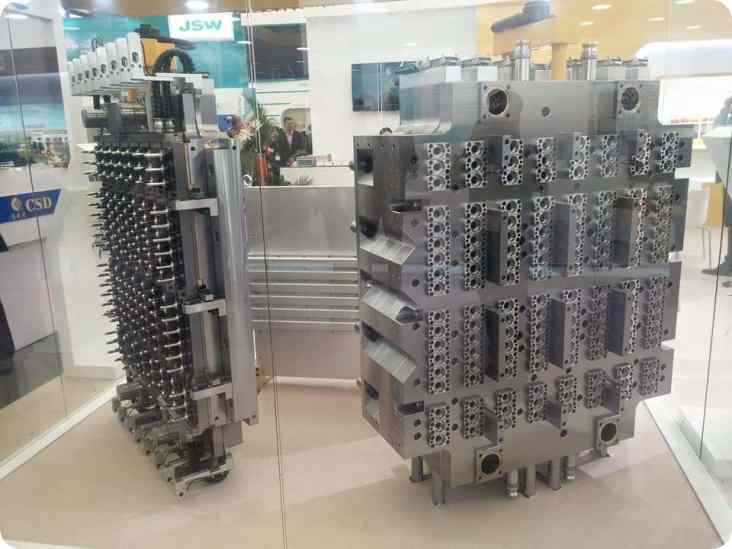
Mold charge is around double for common preform mold Mold life is around 800000 to 1 millon shots Long tail mold need cutting by hand, so need much labor cost.Īnd the Second generation is self-locking common preform mold, this kind mold structure is compared complex, the following photo is for reference.Įccentricity is compared lower, injection production is easier to deal with. Molded preforms don’t have very high quality, usually used for disposible bottle packing. This kind PET preform mold strucure is simple, Eccentricity is compared high, mold production needs worker who has rich experience to handle with.
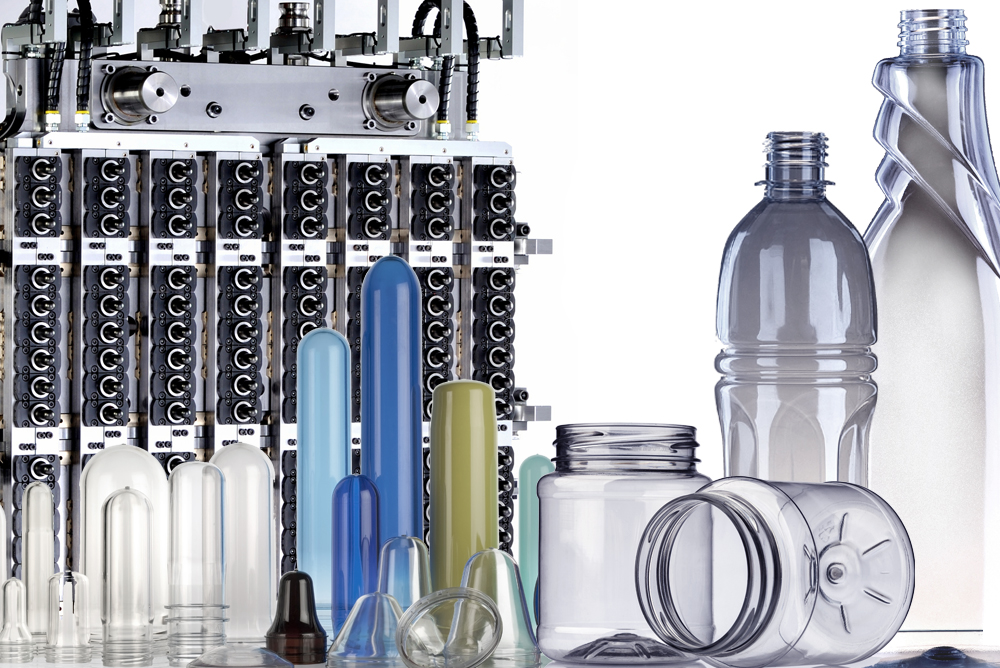
Mold for long tail preform as left sample in following photo, need cutting by hand, mold for short tail preform as middle sample, no need cutting. Take PET Preform Mold for example, the first generation oldest type is common preform mold with short tail or long tail. Nowadays technology develop so fast, mold strucutre change in big extent also.
